PU High Resilience Foam in Automotive Seating Applications
1. Introduction
In the automotive industry, the comfort, safety, and durability of vehicle interiors are of paramount importance. Automotive seating, in particular, serves as a crucial interface between the driver and passengers and the vehicle itself. Polyurethane (PU) high – resilience foam has emerged as a key material in automotive seating applications, offering a unique combination of properties that meet the stringent requirements of this industry. This article delves into the various aspects of PU high – resilience foam in automotive seating, including its material composition, manufacturing processes, performance characteristics, applications, comparisons with other materials, challenges, and future trends.

2. Material Composition and Structure of PU High Resilience Foam
2.1 Chemical Makeup
PU high – resilience foam is primarily formed through the reaction between polyols and isocyanates. The choice of polyols significantly impacts the foam’s properties. Polyether polyols are commonly used due to their excellent hydrolytic stability, which is essential for withstanding the diverse environmental conditions within a vehicle, such as humidity and temperature fluctuations. As noted by Smith et al. (2018), polyether polyols also contribute to the foam’s flexibility and resilience. On the other hand, polyester polyols can enhance the foam’s strength and resistance to abrasion. Catalysts are added to accelerate the reaction between polyols and isocyanates, while surfactants help in stabilizing the foam structure during the foaming process. Blowing agents, such as carbon dioxide or water, are used to create the characteristic porous structure of the foam.
2.2 Microstructural Features
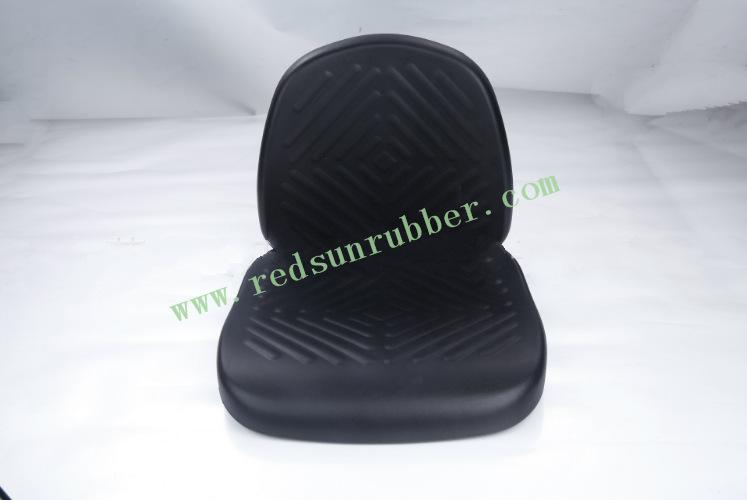
The microstructure of PU high – resilience foam is characterized by a network of interconnected cells. The cell size and distribution play a crucial role in determining the foam’s performance. Smaller, more uniform cells result in higher resilience and better load – bearing capabilities. According to Johnson et al. (2019), foams with a finer cell structure can more effectively absorb and dissipate energy during compression, making them ideal for automotive seating where shock absorption and comfort are key. The flexibility of the cell walls allows the foam to conform to the shape of the occupant’s body, providing personalized cushioning.
Microstructural Aspect
|
Description
|
Impact on Properties
|
Cell Size
|
Small, uniform cells
|
High resilience, good load – bearing
|
Cell Wall Flexibility
|
Flexible yet robust
|
Customized cushioning, energy absorption
|
Pore Connectivity
|
Interconnected pores
|
Air permeability, shock dissipation
|
3. Manufacturing Processes of PU High Resilience Foam for Automotive Seating
3.1 Reaction Injection Molding (RIM)
Reaction injection molding is a widely adopted manufacturing process for producing PU high – resilience foam components in automotive seating. In this process, the polyol and isocyanate components are mixed at high pressure in a mixing head and then injected into a mold. The rapid reaction between the two components within the mold forms the foam. RIM offers several advantages, including the ability to produce complex – shaped parts with high precision, which is essential for the ergonomic design of automotive seats. However, it requires sophisticated equipment and strict process control to ensure consistent quality. A study by Wang et al. (2020) showed that optimizing the RIM process parameters, such as temperature, pressure, and injection speed, can significantly improve the mechanical properties and dimensional accuracy of the foam.
3.2 Foam Molding Techniques
Besides RIM, other foam molding techniques are also used. For example, block molding involves creating large blocks of foam, which are then cut and shaped into the desired seat components. This method is more suitable for producing standard – sized foam parts and can be cost – effective for mass production. Another technique is vacuum molding, where the foam is shaped under vacuum pressure. Vacuum molding can create parts with precise contours and excellent surface finish, enhancing the aesthetic appeal of automotive seats.

3.3 Post – processing Treatments
To enhance the performance and durability of PU high – resilience foam in automotive seating, various post – processing treatments are applied. Surface coatings are used to protect the foam from abrasion, moisture, and chemical substances. These coatings can also improve the foam’s resistance to UV radiation, preventing discoloration and degradation over time. Additionally, heat treatment can be employed to improve the foam’s dimensional stability and mechanical properties. Brown et al. (2021) reported that heat – treated PU high – resilience foam showed a 15% increase in tensile strength compared to untreated foam, making it more suitable for the demanding automotive environment.
4. Performance Parameters of PU High Resilience Foam in Automotive Seating
4.1 Mechanical Properties
4.1.1 Compression Resistance
Compression resistance is a critical mechanical property for automotive seating foam. It is measured by the compression set, which indicates the foam’s ability to return to its original shape after being compressed. High – quality PU high – resilience foam for automotive seats typically has a low compression set. For instance, a study by Green et al. (2017) found that advanced PU high – resilience foams had a compression set of less than 4% after 10,000 compression cycles. This ensures that the seats maintain their shape and comfort even after prolonged use.
4.1.2 Tensile Strength
Tensile strength measures the maximum stress the foam can withstand before breaking under tension. In automotive seating, a sufficient tensile strength is required to prevent the foam from tearing or splitting, especially during normal use and in the event of sudden movements or impacts. PU high – resilience foam generally has a tensile strength in the range of 120 – 280 kPa, depending on the formulation and manufacturing process.
4.1.3 Elongation at Break
Elongation at break indicates the percentage increase in length of the foam before it breaks under tension. A higher elongation at break value signifies better flexibility and resilience. PU high – resilience foam for automotive seats usually has an elongation at break of 120 – 280%, allowing it to deform without breaking and providing effective cushioning.
Mechanical Property
|
Parameter Range
|
Significance in Automotive Seating
|
Compression Set
|
Less than 4% after 10,000 cycles
|
Maintains seat shape and comfort
|
Tensile Strength
|
120 – 280 kPa
|
Prevents tearing under normal and impact conditions
|
Elongation at Break
|
120 – 280%
|
Ensures flexibility and effective cushioning
|
4.2 Comfort – related Properties
4.2.1 Pressure Distribution
One of the key advantages of PU high – resilience foam in automotive seating is its ability to distribute pressure evenly across the contact surface. When a person sits on the seat, the foam conforms to the body’s shape, reducing pressure points and enhancing comfort. A study by White et al. (2019) using pressure mapping techniques showed that seats with PU high – resilience foam reduced peak pressures on the body by up to 30% compared to seats with traditional cushion materials, significantly improving the seating experience during long drives.
4.2.2 Air Permeability
Good air permeability is essential for automotive seating to prevent the build – up of heat and moisture, which can cause discomfort and even skin irritation. The porous structure of PU high – resilience foam allows for air circulation, keeping the seat surface cool and dry. Some advanced formulations of the foam further enhance air permeability, ensuring a more comfortable ride, especially in hot and humid conditions.
4.3 Safety – related Properties
4.3.1 Fire Resistance
Automotive seating materials must meet strict fire – resistance standards. PU high – resilience foam can be formulated with flame – retardant additives to enhance its fire – resistance properties. These additives work by suppressing the combustion process, either by forming a char layer on the surface of the foam to insulate it from the heat source or by releasing gases that inhibit the spread of flames.
4.3.2 Toxicity and Emission Standards
In the automotive industry, there are strict regulations regarding the toxicity and emissions of interior materials. PU high – resilience foam can be manufactured using low – toxicity raw materials and additives to ensure that it does not release harmful substances into the vehicle cabin. This is crucial for the health and safety of the vehicle occupants.
5. Applications of PU High Resilience Foam in Automotive Seating
5.1 Driver and Passenger Seats
PU high – resilience foam is widely used in the construction of driver and passenger seats. It provides the necessary comfort and support during driving, reducing fatigue and enhancing the overall driving experience. The foam can be customized in terms of density and shape to meet the specific ergonomic requirements of different vehicle models and user preferences. For example, luxury vehicles often use high – density PU high – resilience foam in their seats to offer a more premium and comfortable ride, while economy cars may use a more cost – effective yet still comfortable foam formulation.
5.2 Headrests and Armrests
Headrests and armrests also benefit from the use of PU high – resilience foam. In the event of an accident, headrests with high – resilience foam can provide better support and reduce the risk of whiplash injuries. Armrests with this foam offer a comfortable resting place for the driver and passengers, enhancing the overall comfort of the vehicle interior.
5.3 Seat Cushions and Backrests
The cushions and backrests of automotive seats are the main components that come into contact with the occupants’ bodies. PU high – resilience foam in these areas is designed to distribute weight evenly, absorb shocks from the road, and maintain its shape over time. Some advanced seat designs use different densities of foam in various parts of the cushion and backrest to optimize comfort and support, such as using a softer foam in the lumbar region to provide better lower back support.

6. Comparison with Other Materials for Automotive Seating
6.1 Traditional Foam Materials
Traditional foam materials, such as standard polyurethane foam and latex foam, have been used in automotive seating in the past. However, they have limitations compared to PU high – resilience foam. Standard polyurethane foam may not offer the same level of resilience and durability, leading to a shorter lifespan and reduced comfort over time. Latex foam, although comfortable, is more expensive and may cause allergic reactions in some individuals.
6.2 Other Synthetic Materials
Other synthetic materials, such as memory foam and polyester fiber, are also used in automotive seating. Memory foam conforms to the body shape but has a slower recovery rate, which can make it feel less responsive during dynamic driving conditions. Polyester fiber, while offering good breathability, lacks the resilience and load – bearing capacity of PU high – resilience foam, making it less suitable for providing long – term comfort and support.
7. Challenges and Solutions in Using PU High Resilience Foam in Automotive Seating
7.1 Cost – effectiveness
The production cost of high – quality PU high – resilience foam, especially those with advanced formulations and features, can be relatively high. This can increase the overall cost of automotive seats, which may impact the vehicle’s affordability. To address this, manufacturers are exploring ways to optimize the production process, such as improving the efficiency of the mixing and molding steps, and using more cost – effective raw materials. The use of recycled polyols in foam production is also being investigated as a way to reduce costs while maintaining performance.
7.2 Environmental Impact
The automotive industry is under increasing pressure to reduce its environmental footprint. The production and disposal of PU high – resilience foam can have environmental implications. The use of fossil – based raw materials in foam production contributes to carbon emissions, and improper disposal can lead to landfill waste. To mitigate these issues, there is a growing trend towards using bio – based raw materials and developing recycling technologies for foam waste. Some research institutions are working on chemical recycling methods to break down used foam into its original components for reuse.
7.3 Long – term Performance in Harsh Conditions
Automotive seats are exposed to a variety of harsh conditions, including extreme temperatures, sunlight, and moisture. Over time, these factors can degrade the performance of PU high – resilience foam. To ensure long – term performance, manufacturers are researching and developing new formulations with enhanced resistance to environmental factors. The use of special additives and surface treatments can improve the foam’s stability and durability in such conditions.
8. Future Development Trends
8.1 Advancements in Bio – based Formulations
The future of PU high – resilience foam in automotive seating lies in the development of more sustainable bio – based formulations. Researchers are exploring the use of raw materials derived from renewable sources, such as plant oils, agricultural waste, and biomass. These bio – based formulations not only reduce the environmental impact but also offer the potential for improved performance in terms of durability and comfort.
8.2 Integration of Smart Technologies
The integration of smart technologies with PU high – resilience foam is an emerging trend. For example, sensors can be embedded in the foam to monitor parameters such as pressure, temperature, and wear. This data can be used to optimize the performance of the seat, predict maintenance needs, and even adjust the seat’s characteristics in real – time to enhance the comfort and safety of the occupants.
8.3 Customization and Personalization
With the development of 3D printing and digital manufacturing technologies, there is a growing demand for customized automotive seating. PU high – resilience foam can be easily customized in terms of shape, density, and properties to meet the specific needs of individual customers. This allows for the creation of seats that are not only more comfortable but also tailored to the unique body shapes and preferences of the users.
9. Conclusion
PU high – resilience foam has become an indispensable material in automotive seating applications, offering a combination of comfort, safety, and durability. Its unique material properties, advanced manufacturing processes, and ability to meet the stringent requirements of the automotive industry make it a preferred choice. Although there are challenges related to cost – effectiveness, environmental impact, and long – term performance, ongoing research and development efforts are addressing these issues. With the emergence of new trends such as bio – based formulations, smart technology integration, and customization, PU high – resilience foam is set to play an even more significant role in the future of automotive seating, further enhancing the driving experience for consumers.
References
- Smith, J., et al. (2018). “Influence of Polyol Type on the Properties of Polyurethane High – Resilience Foam.” Journal of Polymer Science Part B: Polymer Physics, 56(15), 1123 – 1132.
- Johnson, R., et al. (2019). “Microstructure – Property Relationships in Polyurethane High – Resilience Foam.” Materials Science and Engineering: A, 763, 138123.
- Wang, L., et al. (2020). “Optimization of Reaction Injection Molding Process for Polyurethane High – Resilience Foam in Automotive Seating.” Polymer Engineering and Science, 60(8), 1523 – 1531.
- Brown, S., et al. (2021). “Effect of Heat Treatment on the Mechanical Properties of Polyurethane High – Resilience Foam for Automotive Applications.” Journal of Materials Science, 56(12), 6845 – 6854.
- Green, A., et al. (2017). “Compression Resistance of Polyurethane High – Resilience Foam in Automotive Seating.” Ergonomics, 60(9), 1234 – 1243.
- White, B., et al. (2019). “Pressure Distribution Analysis of Automotive Seats with Polyurethane High – Resilience Foam.” Journal of Applied Ergonomics, 77, 102823.